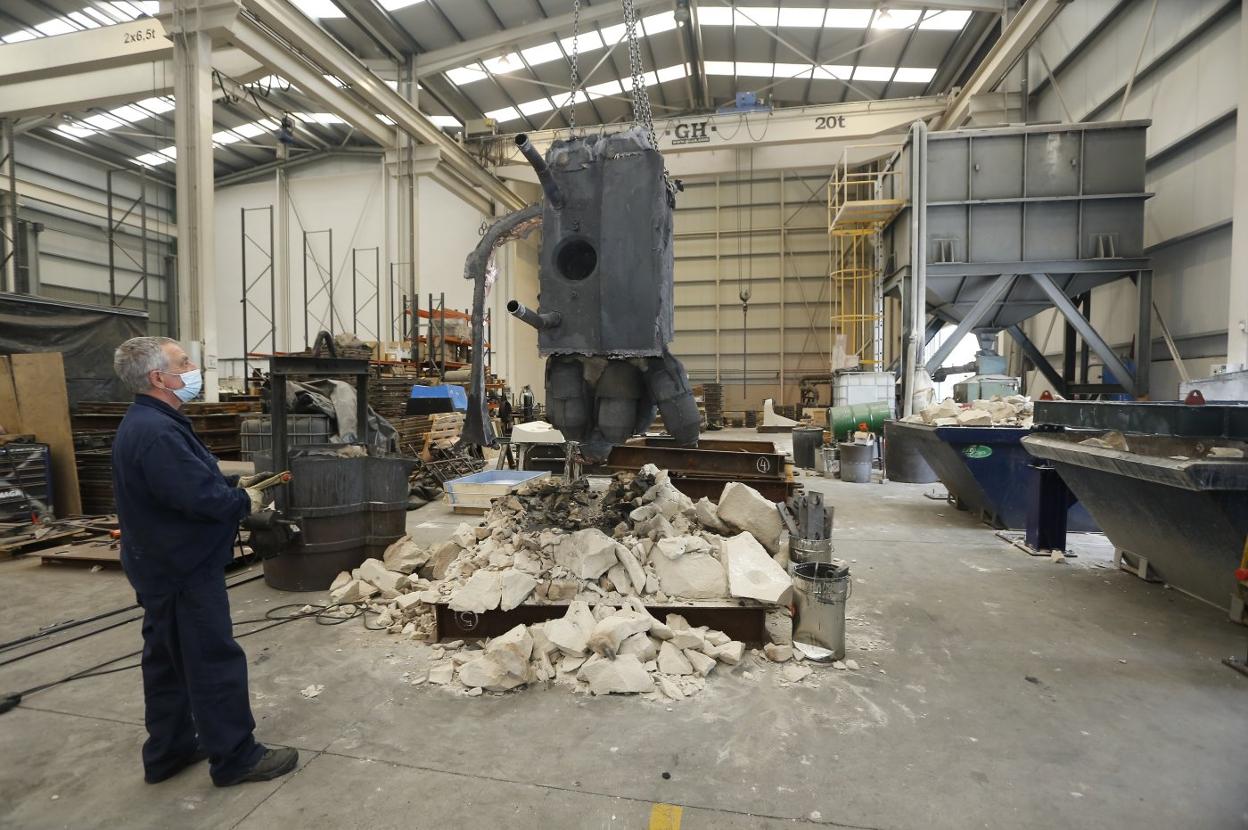
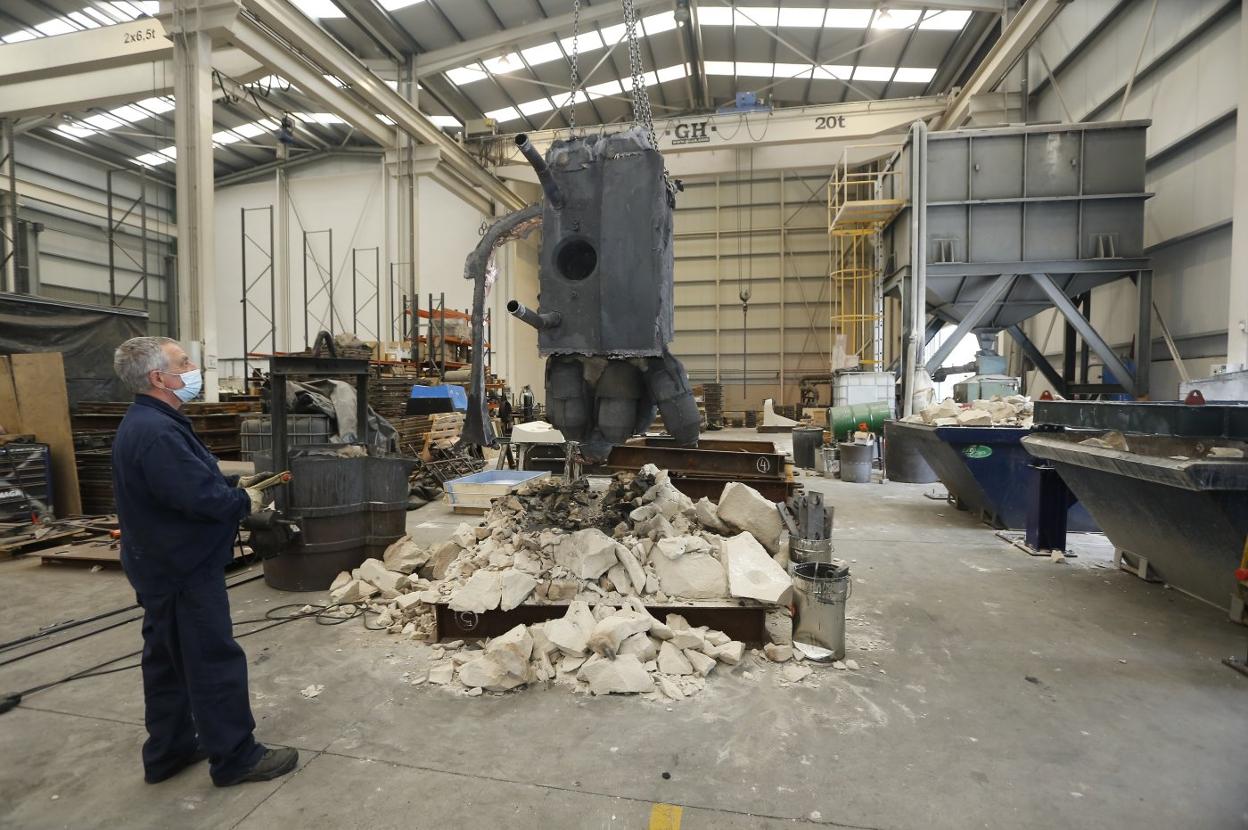
Secciones
Servicios
Destacamos
El viejo túnel ferroviario de Canfranc está emplazado en el Pirineo aragonés y sirve de nexo de unión entre España y Francia. Dejó de emplearse ... en la década de los 70 debido al derrumbe de uno de los puentes en la parte gala, causado por el descarrilamiento de un tren, pero a día de hoy tiene un nuevo uso mucho más intrigante y prometedor. En la actualidad aloja uno de los laboratorios de baja radiación más importantes del mundo.
Allí, a 850 metros bajo tierra, se levanta la infraestructura singular que en la actualidad se conoce como Laboratorio Subterráneo de Canfranc (LSC). Una instalación especializada en experimentos que necesiten estar situados en el 'silencio cósmico' que proporciona la profundidad de la montaña. Una de las características es que en él se desarrollan y construyen detectores ultrasensibles, capaces de localizar fenómenos a escala subatómica tan débiles como puede ser la desintegración de un único núcleo. El desarrollo de estos instrumentos supone un desafío científico y tecnológico que abarca decenas de años y trasciende la vida profesional de sus creadores. Muchos de los académicos que participan consagran su carrera al desarrollo de un sistema que no estará terminado cuando se jubilen. Durante este tiempo se ponen en marcha soluciones técnicas que imponen un grado de exigencia máximo sobre las tecnologías de fabricación y que lleva a investigadores e industriales a colaborar juntos para poder superar las dificultades.
14toneladas pesan las piezas fundidas por WeCo y enviadas al Pirineo.
El experimento de Física de Partículas más relevante que se aloja en el LSC (y por lo tanto en suelo español) es NEXT, un instrumento diseñado para identificar un raro proceso de desintegración nuclear conocido como desintegración doble beta sin neutrinos. La confirmación de la existencia de este proceso, que no ha sido detectado nunca antes, constituirá uno de los grandes hitos de la Física Moderna, con profundas implicaciones en las teorías científicas más importantes, como son el Modelo Estándar y el Big Bang.
Un ambicioso camino para descubrir los orígenes del universo en el que Cantabria ha aportado su granito de arena, una contribución que previsiblemente tendrá continuidad, según avanzan fuentes del LSC. ¿De qué forma? Pues a través de la participación de la compañía Welding Copper (WeCo), firma especializada en la fundición de materiales no férricos enclavada en el Parque Empresarial Besaya, en la localidad de Reocín. «La fabricación de las piezas de blindaje no hubiese sido posible sin poder contar con la infraestructura y, sobre todo, la experiencia de industriales altamente especializados y cualificados. En esta tarea, la contribución cántabra ha resultado fundamental: las piezas de cobre ultrapuro han sido fundidas en las nuevas instalaciones de WeCo-Welding Copper. Sin duda, la tarea de mayor dificultad ha recaído sobre la fundición, en donde se han llegado a conformar piezas de hasta dos toneladas acabadas de cobre puro. La tarea se basa en elaborar un molde de arena con la forma adecuada, en el cual se vierte el material fundido. Sólo la experiencia y los procesos exclusivos desarrollados por WeCo han permitido llegar a piezas con la calidad suficiente para ser integradas en el detector NEXT. A partir de aquí, WeCo se perfila como un colaborador fundamental para la construcción de la versión final de NEXT. Para ello, la empresa ya se está planteando modernizar y ampliar sus instalaciones y procesos», explican los impulsores del proyecto científico.
Conceptualmente, el detector es un depósito que contiene una cierta cantidad de gas xenon a alta presión, y que está dotado de una serie de dispositivos que permiten amplificar y detectar las señales que se generen en el gas. Si la reacción doble beta tiene lugar, alguno de los átomos de xenon se romperá de forma espontánea, transformándose en un átomo de bario.
El desafío técnico del detector es gigante: la desintegración doble beta sin neutrinos es tan rara que, si se observan todos los átomos contenidos en una tonelada de material, sólo uno de ellos se desintegrará por tonelada al año.
Otro factor fundamental es el ruido que percibe el dispositivo, proveniente de otros procesos, principalmente de la radiación cósmica y de la desintegración de átomos radioactivos presentes en la roca del laboratorio y en los propios materiales con los que está construido el detector.
Reducir al mínimo el ruido es importante para evitar que el sistema automático de clasificación de señales se sature y pueda identificar las escasas señales útiles. Para esta tarea resulta fundamental recurrir a la técnica del blindaje, mediante la cual una parte interna del detector se forra con un material ultra-puro, en este caso cobre, que es capaz de absorber una buena parte de las partículas provenientes del exterior, incluyendo las emitidas por las propias paredes del detector.
Javier Bolado, CEO de Welding Copper, explica que «hemos hecho toda la fundición de cobre. La experimentación se hace dentro de una especie de vasija, por lo que se montan piezas. Han sido 14 toneladas de producto acabado y supone una parte importante. Lo que necesitaba el proyecto es que una fundición lo tratara de golpe. Es decir, no se podía partir de cobres fabricados. Atlantic Copper nos mandó el cobre puro y nosotros lo fundimos de golpe», anota.
Bolado admite la exclusividad de las actividades que se llevan a cabo hoy en día en Reocín. «No encontraban a nadie para hacer el trabajo. Al principio descartamos el encargo por sus requisitos técnicos. Después empezamos a hablar y vimos que era posible. Al estar inmerso el Ministerio de Industria, les interesaba también que los trabajos se acometieran en España, por lo que al final ganamos la licitación».
En un contexto de evidente incertidumbre para la industria nacional por el encarecimiento de las materias primas y la energía, compañías como Welding Copper miran al futuro con optimismo y tranquilidad gracias a la demanda que reciben sus exclusivas actividades de fundición. Con 40 trabajadores en plantilla y nuevas perspectivas de contratación, el CEO de la organización, Javier Bolado, señala que «tenemos un proceso en el que conseguimos trabajar cobre puro sin ningún aditivo metálico de desidoxidación. Esa es la parte importante por ejemplo en proyectos como NEXT» en el laboratorio de Canfranc.
Ese proceso de meter y sacar de un horno cobre puro es algo muy específico. «No lo está haciendo nadie en España», presume el empresario.
Las consecuencias, evidentes. «Estamos creciendo y hemos accedido recientemente a las nuevas instalaciones. Diría que tengo ya cerrado prácticamente el trabajo para 2023. Es un poco locura. Nuestra mayor problemática es encontrar gente que quiera trabajar».
Con esta perspectiva, «la idea es invertir en tecnología. Estamos mirando varios procesos para mejorar nuestra actividad», agrega.
Por una cuestión económica, el instrumento de Canfranc se desarrolla en varias etapas. Las fases pequeñas, menos costosas, permiten validar las tecnologías antes de construir la versión más grande, que es la que puede proporcionar resultados científicos relevantes. En la actualidad NEXT ha alcanzado su etapa intermedia y contendrá 100 kilos de xenon. Incluso a esta escala, el blindaje de cobre ultra puro está compuesto por piezas de entre cientos de kilos y varias toneladas de peso. Esta escala es la primera en la que el desafío industrial se vuelve relevante y se hacen evidentes todos los problemas que plantea la construcción.
El objetivo, un aprendizaje que sirva para desarrollar y fabricar de forma más eficiente la versión final de NEXT, de una tonelada de Xenon.
¿Ya eres suscriptor/a? Inicia sesión
Publicidad
Publicidad
Te puede interesar
Publicidad
Publicidad
Esta funcionalidad es exclusiva para suscriptores.
Reporta un error en esta noticia
Comentar es una ventaja exclusiva para suscriptores
¿Ya eres suscriptor?
Inicia sesiónNecesitas ser suscriptor para poder votar.